Features and Software
Overview
Figure 1: TwinProx dual channel proximity probe module.
Proximity probes are used to monitor large industrial machines such as centrifugal compressors, motors, pumps, steam turbines, hydro turbines, generators, gearboxes, fans, and reciprocating compressors. Case-mounted accelerometers are unsuitable for monitoring these machines due to the large difference in the ratio between the small rotor mass and the much larger stator mass. The same vibration measured by a case-mounted accelerometer would be insufficient to alert the user to the onset of catastrophic damage.
Machine Saver’s TwinProx-VO delivers two probe drivers with advanced customization features tuned to our customers' specific applications.
Compatible with existing API670 style proximity probe systems such as 3300XL® and NSV®, TwinProx-VO is designed for larger critical machines and balance of plant machines with oil-lubricated journal bearings and is helping many plants monitor shaft vibration relative to the sleeve bearing.
Figure 2: Typical TwinProx installation on large machine train.
Note: TwinProx-VO (Voltage Out) does not daisy-chain such as the TwinProx-MB (Modbus)
Features and Benefits
TwinProx-VO is a dual channel non-contact proximity module configurable as two probe drivers. TwinProx-VO also has a MODBUS RS485 connection to field customize for different probe series, system lengths and shaft materials.
Quality life expectancy from manufacturer of 10 years.
CSA, UL, IECEX, CE, ATEX certified (pending approval).
Suitable mounting options and approvals for hazardous locations.
Designed and manufactured in the United States of America.
Designed specifically for customers' machine applications.
Ability to digitally accommodate a variety of target materials.
Simplified probe gap adjustment using multi-color LEDs.
Compatible to other API670 style proximity probe systems such as ¹ 3300XL® and NSV®.
Color-coded wire terminals and cables.
Reverse mount probe housing and DINrail mounting options.
Modbus RTU field configuration and calibration capability.
Interface directly to plant PLC, DCS and other data acquisition systems.
Taring feature ensures long runs do not sacrifice the voltage out readings such as existing competitor drivers.

Figure 3: TwinProx application motion reference.
Specifications
Power |
+ 24 VDC - 24 VDC |
Channels | 2 |
Input | 2 API670 style non-contact proximity probes |
Output |
Voltage (0 to 20 V) |
Communication Protocol (Configuration and Calibration) | Modbus RTU Baudrate: 115200 Parity: None Handshakes: None Data Bits: 8 Stop Bits: 1 |
Temperature Range |
Standard: -40°F (-40°C) to +185°F (85°C)
High-Temperature Option: +212°F (+105°C) *Consult Factory for High Temperature Applications |
Mounting Options | 35mm DINrail Baseplate + Fastener |
Display / Indicators | 3 high intensity, multi-color LEDs (system and probe status) |
Enclosure | PBT (Thermoplastic Polymer Blend) |
Hazardous Area Approvals |
CSA, cUL, IECEx, Class I Division 2 Groups A-D (pending) CE and RCM (pending) |
Ranges |
70 mils (1778 microns) 160 mils (4064 microns) |
Compatible Probe Series |
3300 8mm 3300 11mm (option) 3309 Focus View 5mm 7200 8mm |
System Lengths |
1 meter 5 meter 7 meter (Focus View only) 9 meter * Consult factory for custom system lengths. |
Target Materials |
Standard: ASTM 4140
*Consult factory for other target materials |
Accuracy | +/- 2% of full scale |
Linearity | +/- 1 mil best straight-line fit |
Resolution |
0.0002” (5um) |
Frequency Response |
0 – 5,000Hz |
IP Rating |
IP64 |
Humidity | 99% condensing |
Terminals | > 15 Newton hold force |
Programmable | TwinProx ship configured based on user preferences. All functions can be set using the user interface software. |
Weight | 4.8 ounces (136 grams) |
Dimensions
Figure 6: Dimensional Drawing
Field Customization Options
TwinProx configuration software is made for our customers that require advanced configurations.
The simple and intuitive user interface allows:
- Configuring TwinProx modules
- Linearization
- Application settings
- Probe gap settings
Field Linearization
TwinProx is typically used with ANSI 4140 shaft material but may also be linearized in the field for other ferrous metal alloys like stainless steel, K-MONEL, INCOLOY and other. This allows technicians to react to uncommon target materials should they find them during an installation.
This technique is available to do either manually, using a traditional static calibrator, or it can be done automatically, using Machine Saver's Probulator (a high precision target driving device).
Figure 5: The TwinProx software features a simple, intuitive user interface that makes it easy to configure TwinProx in the field.
Probe Gap Distance
Each TwinProx channel has an adjustable, user-defined probe gap distance. When installing the proximity probe in the bearing housing, the TwinProx multi-color LED associated with that channel will flash to indicate that the probe is installed the correct distance from the shaft as shown on Figure 8.
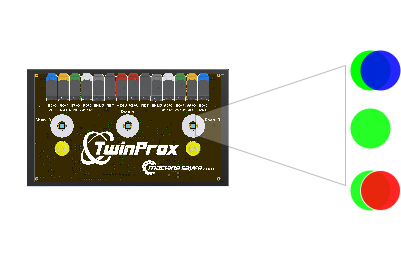
Figure 8: Multi-color LED Instructions for Gap setting on Channel B
LED Status | Definition | Remedy |
Flashing Green / Blue | Probe gap is larger than the customer defined distance. | Screw the probe so that the tip moves toward the shaft until the LED becomes solid green. |
Solid Green | Probe gap is equal to the customer defined distance. | None, this is the goal of gapping the probe. |
Flashing Green / Red | Probe gap is smaller than the customer defined distance. | Unscrew the probe so that the tip moves away from the shaft until the LED becomes solid green. |
Applications
Radial Vibration
Measures the movement of a machine's shaft using AC and DC components of the transducer signal. Available outputs:
Dynamic data for analysis
Displacement overall
Configuration software can be configured with different options:
Overall displacement vibration monitoring
Axial Thrust Position
Position measurements utilize the DC component of the transducer signal, the measurement unit is Mils or Microns.
Configuration software can be configured with multiple options:
Axial thrust position monitoring
Speed
Measures the machine speed in revolutions per minute (rpm), cycles per minute (cpm) or Hertz (Hz).
Configuration software can be configured with four different functions:
Speed monitoring
Long Extension cable runs (Taring feature)
For longer power and signal cable run distances, TwinProx-VO has a voltage drop tare feature that ensures that voltage drops due to long cable runs may be corrected. This industry first tare feature ensures accurate readings at the monitor up to 300 meters (1000 feet) from the TwinProx-VO
Phase Reference
Presents live data feed of vibration phase data as the key or key way passes the phase reference probe.
How to Order
Product Code | Probe Series and Tip Diameter | System Length | Special Application |
2PRX-VO | A | B | C |
*2PRX refers to TwinProx model prefix.
Probe Series and Tip Diameter
A |
0 = 3300 8mm (Default) 1 = 3300 11mm 2 = 3309 5mm Focus View |
System Length
B |
5 = 5 Meter (Default) 1 = 1 Meter 7 = 7 Meters (3309 Series Only) 9 = 9 Meters |
Special Application
C | 00 = No Special (Default) |
Accessories
- Static Calibrator (Manual Calibration Tool)
- Probulator (Automated Calibration Tool)
- ProxBox (Reverse Mount Probe Housing)
- TwinProx Enclosure
- Proximity Probes
- Extension Cables
- Probe Brackets
Manuals and Software
The latest versions of Machine Saver TwinProx configuration software and user instructions can be downloaded from Machine Saver's Library: https://library.machinesaver.com/books/
No Comments