TwinProx Universal Proximity System (Installation Manual)
TwinProx_MB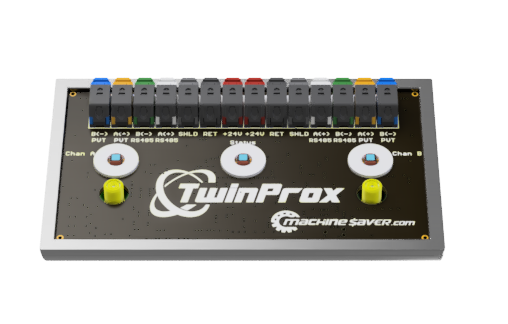
TwinProx_VO
Installation Manual
The TwinProx family consists of 2 devices, the TwinProx_MB and the TwinProx_VO.
Both the TwinProx_MB and TwinProx_VO are dual channel proximity transmitter system which allows users to use a variety of probe and extension cable combinations (from a variety of traditional manufacturers) without the hassle of using specific drivers and transmitters for each series, tip diameter and extension cable length. The TwinProx_MB and TwinProx_VO both are capable of being setup using an intuitive user interface via an RS485 connection to a computer. All functions are also settable using Modbus read/write commands from any Modbus master. The TwinProx_VO provides a voltage output so customers used to the Proximitor or Probe Driver interface may continue operating within their comfort zone for alarms and shutdown.
Safety Terms and Symbols
Terns that appear in this manual requiring special attention include:
-
WARNING: Warning statements identify conditions or practices that could result in injury or loss of life.
-
CAUTION: Caution statements identify conditions or practices that could result in damage to the product, loss or corruption of data, or damage to the environment or other property.
-
NOTE: Notes identify material or special interest or importance to the user, not including caution or warnings.
Symbols that may appear on the product and/or this manual include:
General Safety Summary
Review the following safety precautions to avoid injury and prevent damage to this product or any products connected to it.
- Use Only as Specified
To avoid any potential hazards, use this product only as specified.
Only qualified personnel should perform installation and uninstallation procedures. - Observe All Terminal Ratings
To avoid fire or shock hazard, observe all ratings and markings on the product.
Consult the individual sections of this manual for further ratings information before making connections of product. - Avoid Exposure to Circuitry
Do not touch exposed electrical connections and components when power is present. - Do not Operate with Suspect Failures
If you suspect there is damage to this product, have it inspected by qualified personnel.
Receiving, Inspecting and Handling the System
Machine Saver ships the probe, extension cable, and TwinProx transmitters as separate units that the user interconnects at the installation site. Carefully remove all equipment from the shipping containers and inspect it for shipping damage. If you see shipping damage, file a claim with the carrier and submit a copy to Machine Saver Inc. Include part numbers and serial numbers on all correspondence. If no damage is apparent and the equipment is not going to be used immediately, return the equipment to the shipping containers and reseal until ready for use. Store the equipment in an environment that is free from any potentially damaging conditions such as extreme temperature, excessive humidity, or a corrosive atmosphere.
Overview
Machine Saver's TwinProx System comes in two versions:
- 2PRX-MB = Dual Proximity Transmitter. A Modbus RTU Slave for Setup and Modbus Output for Monitoring
- 2PRX-VO = Dual Proximity Probe Driver.
The following sections cover each of these in more detail.
2PRX-MB
The 2PRX-MB signal format is for use when vibration, axial position, rotational speed, or phase measurements will be directly connected to a Modbus Master (PLC, DCS, SCADA system) or other instrumentation
that accepts Modbus RTU (RS485) inputs.
It is powered by +24 VDC. Two optional wires for a private bus can be used with a monitoring system within 20 meters (65 ft) typically used when 360 degree phase analysis is required. The device is configurable to function as either a radial vibration transmitter (peak‐peak vibration displacement amplitude), as an axial position transmitter (with average displacement distance probe gap), as a rotational speed transmitter (shaft speed), and/or as a 360 degree phase analysis transmitter (syncs the analysis data from all the TwinProx devices on the same machine train --- private bus).
2PRX-VO - Wire Vibration / Position / Speed Transmitter
The 2PRX-VO signal output is compatible with industry-standard continuous-vibration monitoring systems and is the format specified in API Standard 670. It uses ‐24VDC excitation and provides the output signal in mV/mm, typically 7.87 mV/mm (200mV/mil) for 5 mm and 8mm probes and 3.94 mV/mm (100 mV/mil) for 11 mm probes.
Installation
Probe Installation
Mount the probe in a simple bracket in a tapped hole in the bearing cap or by means of a Reverse Mount Probe Housing. The latter arrangement provides an easy means to adjust the probe gap, especially where the target is some distance from the outside surface of the machine.
When inserting the probe into the machine please refer to the user interface Probe Gap instructions. If possible, set the probe gap while the machine is shutdown, to avoid the danger of damaging the probe in the event that it touches the shaft.
Connect the probe to the driver/transmitter using the proper extension cable. If a connector must be replaced, the overall length of the probe or extension cable can be reduced by 2” total without adversely affecting the calibration and linearity. Insulate the probe connector/extension cable connector junction with the connector insulator.
Radial Vibration Measurements
For radial vibration measurements, mount the probe perpendicular to the shaft with the
probe tip approximately 0.050” (1.25 mm) from the shaft surface. Provide the probe tip with
sufficient clearance from surrounding metal to prevent an erroneous output. As a minimum,
the clearance diameter should be 0.75” (19 mm) for the full length of the probe tip. See
Figure 1. You can set the probe gap “visually” to the center of its measurement range by
observing the LED color (reference the LED chart Figure) of the appropriate channel on the TwinProx or by monitoring Modbus registers associated with distance (user interface). The preferred static gap range is 0.030” to 0.050”. To prevent cross-feed between two probes mounted in the same vicinity, maintain a minimum 1.0” (25 mm) spacing between the probe tips. See Figure 2.
Figure_2
Axial Position / Thrust Measurements
For thrust measurements ensure the thrust range is within the probe range. Move the machine to ensure the thrust range is set properly within the probe linear range. For position (thrust) measurements, mount the probe with the probe axis parallel to the
shaft and with the probe tip approximately 0.050” (1.25 mm) from the end of the shaft. For 11 mm diameter probes, this distance is approximately 0.088”(2.2mm). Provide the probe tip with sufficient clearance from surrounding metal to prevent an erroneous output. As a minimum, the clearance diameter should be 0.75” (19 mm) for the full length of the probe tip. For an 11mm probe, the minimum clearance should be 0.88” (22 mm). See Figure 1.
You can set the probe gap “visually” to the center of its measurement range by observing the LED color (reference the LED chart Figure) of the appropriate channel on the TwinProx or by monitoring Modbus registers associated with distance (user interface). The preferred static gap range is 0.030” to 0.050”. To prevent cross-feed between two probes mounted in the same vicinity, maintain a minimum 1.0” (25 mm) spacing between the probe tips. For 11 mm probes, this distance is approximately
1.5” (38mm). See Figure 3.
Figure_3
Speed Measurements
For RPM measurements, mount the probe with its axis radial to the shaft with its tip approximately 0.050” (1.25 mm) from the outermost surface of the shaft. The probe tip must be provided with sufficient clearance from surrounding metal to prevent an erroneous output. As a minimum, the clearance diameter should be 0.75” (19 mm) for the full length of the
probe tip. See Figure 4. To prevent cross-feed between two probes mounted in the same vicinity, at least 1.0”
(25 mm) spacing between the probe tips should be maintained. See Figures 5, 6.
The minimum keyway depth is 0.060” (1.5 mm). The minimum keyway width and key width
is the diameter of the probe tip (Figure 7). These minimums will ensure that the transmitter or driver responds properly to the keyway at all RPMs. Some experimentation may be required such as adjusting the min and max thresholds on the user interface, adjusting the probe gap, and/or modifying the keyway dimensions, or some combination thereof.
The probe can be mounted in a simple bracket, in a tapped hole in the bearing cap, or by means of a Reverse Mount Probe Housing. The latter arrangement provides an easy way to adjust the probe gap, especially where the target is some distance from the outside surface of the machine.
When inserting the probe into the machine please refer to the user interface Probe Gap instructions. If possible, set the probe gap while the machine is shutdown, to avoid the danger of damaging the probe in the event that it touches the shaft.
Connect the probe to the transmitter using the proper extension cable such that the combined system length of probe + cable matches the transmitter configuration. Do not change the length of the extension cable from the system, as such action will adversely affect the calibration and linearity. If a connector must be replaced, the overall length of the cable can be reduced by 2” without harm, we recommend using the linearity function from the user interface to verify any modifications to probe lengths or system lengths. Insulate the probe connector / extension cable connector junction with the connector insulator.
Figure_4
Figure_5
Figure_6
Figure_7
Extension Cable Installation
Route the extension cable using the following guidelines:
• Check that the TwinProx settings on the user interface are set to the actual:
Probe Type and Diameter
Extension Cable Length
Each should belong to the same series
• Secure the extension cable to supporting surfaces or places in conduit. Make certain the
cable is not kinked, scraped, nor bent beyond the minimum recommended radius of 1”.
• Secure coaxial connectors between the extension cable and the proximity probe. Connection should be “finger tight” with an additional quarter turn using an open ended 9/32” wrench or equivalent.
• Insulate the connection between the probe lead and the extension cable by wrapping the
connector with Teflon tape and the connector insulator. Avoid electrical tape for insulation because of its tendency to melt and detach over time.
Driver / Transmitter Installation
Mount the driver or transmitter in a suitable enclosure in a location that is compatible with
its environmental specifications. Refer to the datasheet for the environmental specifications.
The driver or transmitter comes with a 35mm DIN rail mount.
Field Wiring Methods
Proper Bend Radius
The wires going to the TwinProx should not be under any constant stress. Cut enough wire to
reach the TwinProx unit with a 1 inch (25 mm) bend radius and never stretch the wire for the connection.
Field Wire Preparation
Connect the field wiring (18 AWG - Power Pair, 20-24 AWG - Communication Pair, 20-24 AWG, 120 Ohm Impedance - Private Bus Pair) in accordance with the below diagrams. No prior preparation is required for solid core wire connecting to TwinProx terminals other than proper wire stripping. For stranded wires, it is recommended to use tinned strands. Tinned wires not only prevent accelerated corrosion against wet and contaminated environments, but also increase the strength of connection. The below diagram shows the difference between tinned and untinned wires.
Installation for Tinned or Solid Core Wires:
- Prepare: Strip the wire back 0.275 inches (7 mm) from the end of the stranded wire, and tin the wires so they become one piece using solder, like in the picture above. If using solid core wire no tinning is necessary, properly strip the wire. Ensure the tinned wire, or solid core wire, is flat at the end, if not, cut the end slightly with right angle wire cutters to make it flat. Strip additional insulation back, if necessary, to obtain, the 0.275 inches (7 mm) bare wire length.
- Push Button Connection: If using a push button connection, push down on the terminal lever, insert the 0.275 inches (7 mm) wire fully, release the terminal lever, and conduct a 2 pound (1 kg) pull test to ensure a secure connection. Do this with each wire. The color coded push button connectors are designed for 15 Newton, 3.3 lbs (1.5 Kg).
An alternative for stranded wire is to use a small connector ferrule (18 AWG) to facilitate the connection.
Installation for Stranded Wire using a Wire Connector Ferrule:
- Prepare: Strip the wire back 0.275 inches (7 mm) from the end of the wire.
- Insert: Slide the stripped end into the connector.
- Crimp: Use an appropriate crimping tool to crimp the connector and the wire together (please note the area to crimp is on the pin).
- Installation: If using a color-coded push button connection, push down on the terminal lever, insert the connector pin fully, release the terminal lever, and conduct a 2 pound (1 kg) pull test to ensure a secure connection. Do this with each wire. The color coded push button connectors are designed for 15 Newton, 3.3 lbs (1.5 Kg).
Installation for Stranded Wires that are not Tinned:
- Prepare: Strip the wire back 0.275 inches (7 mm) from the end of the stranded wire, like in the picture above. If you are using stranded wire that is not tinned, be sure to twist the wires, to ensure all of the wires enter the connector. Check that the wire end is flat, if not, cut the end slightly with right angle wire cutters to make it flat. Strip additional insulation back, if necessary, to obtain the 0.5 inch (13 mm) bare wire length. All of the strands of wire should go to the bottom of the connector.
- Push Button Connection: If using a push button connection, push down the terminal lever, insert the 0.315 inches (8 mm) wire fully, release the terminal lever, and conduct a 2 pound (1 kg) pull test to ensure a secure connection. Do this with each wire. The color coded push button connectors are designed for 15 Newton, 3.3 lbs (1.5 Kg).
2PRX-MB Field Wiring Installation
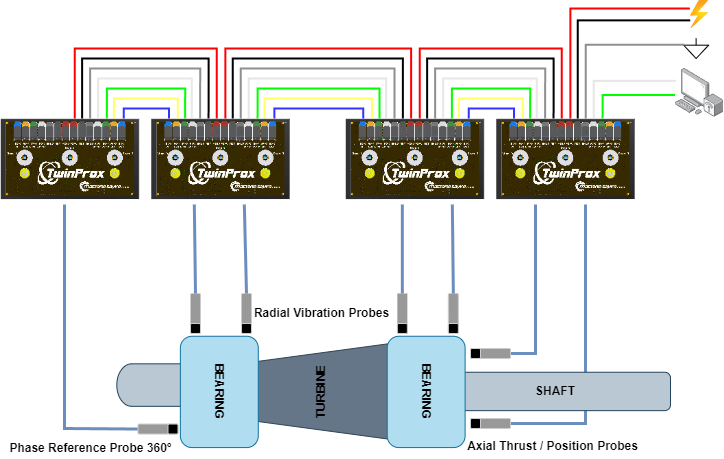
2PRX-VO Field Wiring Installation
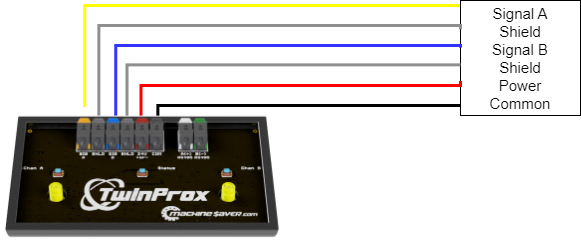
Hazardous Area Installations
Special Conditions of Safe Use
Mount the TwinProx in a separate enclosure capable of withstanding a 7 joule impact and providing a minimum ingress protection of IP54.
The TwinProx cannot be repaired in the field. Replace a failed TwinProx with with an equivalent unit.
Do not expose the TwinProx to dust conditions.
Do not install the TwinProx where it may be subjected to mechanical and excessive thermal stresses or where it may be attacked by existing or forseeable aggressive substances.
Install the TwinProx such that its terminals are protected to at least IP20.
Protect the plastic TwinProx enclosure from impact and friction.
WARNING: TO PREVENT IGNITION OF FLAMMABLE OR COMBUSTIBLE ATMOSPHERES, DISCONNECT POWER BEFORE SERVICING.
WARNING: TO PREVENT IGNITION OF FLAMMABLE OR COMBUSTIBLE ATMOSPHERES, READ, UNDERSTAND, AND ADHERE TO THE MANUFACTURER'S LIVE MAINTENANCE PROCEDURES.
CALIBRATION AND SIGNAL ANALYSIS
General
Factory calibrated units are for use with the specified probe, extension cable and target part numbers. Use the User Interface software to configure un-configured units before putting into service. For maximum accuracy, calibrate the driver with the probe
and cable to be used.
CAUTION: Do not connect test equipment or cables to the driver unless the area has been determined to be non-hazardous.
Environmental Information
This electronic equipment was manufactured according to high quality standards to ensure safe and reliable operation when used as intended. Due to its nature, this equipment may contain small quantities of substances known to be hazardous to the environment or to human health if released into the environment. For this reason, Waste Electrical and Electronic Equipment (commonly known as WEEE) should never be disposed of in the public waste stream. The “Crossed-Out Waste Bin” label affixed to this product is a reminder to dispose of this product in accordance with local WEEE regulations. If you have questions about the disposal process, please contact Machine Saver Inc. Customer Service.
All trademarks, service marks, and/or registered trademarks used in this document belong to Machine Saver Inc. except as noted below:
© 2023, Machine Saver Inc. All rights reserved.
5-11-2023
No Comments