Metric Drill + Tap (Best Method for Frequency Response)
Captive Mounting Bolt M6-1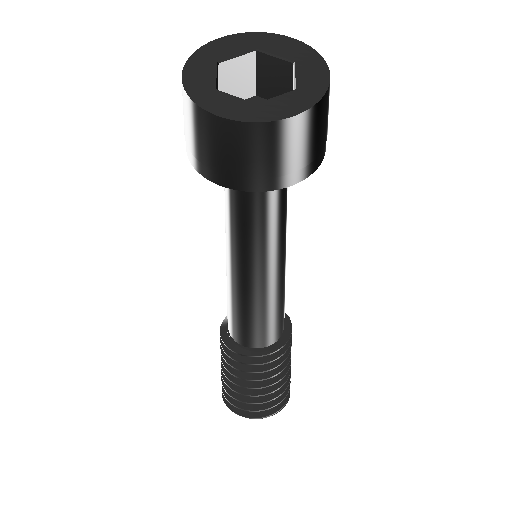
Tools Required
- Power Drill
- 5.0mm Allen Wrench/Hex Key
- 5.0mm (13/64") Drill Bit
- ANSI M6x1 Steel Tap, 3-4 Flute, Right-Hand Thread
- Captive M6-1 Mounting Bolt
- Loctite Threadlocker 242 (Blue/Removable)
- Torque Wrench
Procedure
- Choose mounting location. Accelerometer/Sensor Mounting Location Selection
- Verify the machine casing is thick enough to drill in 7.65mm (0.3 inches).
If the casing is not thick enough, choose a different mounting method. - Use the 5.0mm (13/64") drill bit to drill into the machine casing 7.65mm (0.3 inches).
The hole should be perpendicular to the face of the machine. - Use the ANSI M6-1 tap to cut the threads into the drilled hole. Be sure to keep the tap perpendicular to the face of the machine while tapping to avoid a crooked thread.
- After tapping completely to the bottom of the 7.65mm (0.3 inches), clean any metal shavings from the hole and clean with a Q-Tip and degreaser.
- Insert 5.0mm Allen Wrench/Hex Key into the hex depression on the captive M6-1 mounting bolt.
- Fasten the 1/4"-28 captive mounting bolt into the center threads of the TriVibe, starting on top of the sensors (the side with an LED).
When completely inserted, the threaded tip of the mounting bolt should stick out the bottom of the TriVibe (opposite sied of the LED. - Add a dab of Loctite Threadlocker 242 to the exposed threads.
-
This step is important because, over time, movement can cause the mounting bolts to become loose and result in improper vibration levels.
- Insert the wet, loctite-ed threads into the newly tapped hole.
- Rotate the Allen Wrench/Hex Key clockwise to tighten until the torque on the Allen wrench is 25.0 lb-in (3.0 N-m).
-
Do not over tighten because excess external pressure/force on the housing can cause damage to the internal chops and sensors of TriVibe.
No Comments